Day to day
Working at lightspeed involves being courageous, devising unorthodox solutions, and making bold moves. It requires streamlining processes and making sure that team members from different parts of Pfizer—from the technicians on the manufacturing floor to chemists, engineers, and senior executives—are all on the same page.
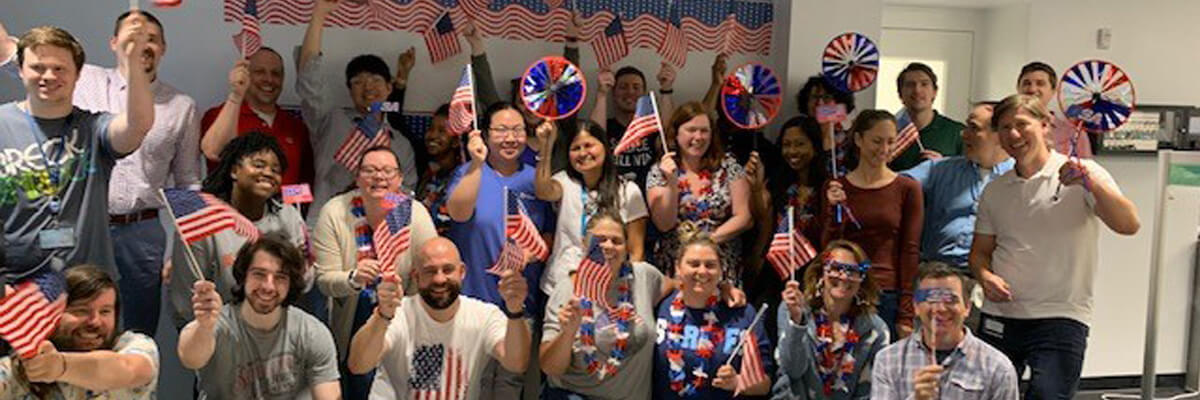
To advance Pfizer’s gene therapies toward the market, the team at Sanford is doing all of this in a constantly changing environment where every day is different, bringing its own unique challenges.
“We hold a daily meeting at 7 a.m., where team members discuss what we’ve learned from the previous day, who will fulfill which roles, and anything that might hinder our ability to perform our work successfully,” Megan says. “And then we get to work.”
On the manufacturing floor, Megan’s team is all about continuous improvement. They are constantly communicating, checking in with each other throughout the day, and refining procedures.
Each day is different, and the team leverages valuable experiences on the manufacturing floor to implement robust improvements.
It’s not always easy, especially when things do not go as planned. One such instance was a setback that occurred with cell culture during an engineering run, a process development step that tests whether the manufacturing process for a particular medicine is scalable.
Terrari’s team noticed that the cells in a large bioreactor were not growing well—this was a critical issue as these cells are crucial in the manufacturing of viral vectors, which are used to carry gene therapies into the human body. Rather than terminating that batch, they investigated why the cells weren’t growing.
“We don’t just want to give up and start over without knowing what went wrong. We want to find the root cause of the problem,” Terrari says. “My role in that situation was to pull all of these scientists and engineers together, balance their different expertise and personalities, and drive them toward a solution in a collaborative environment.” Together, the team pinpointed the root cause, adding to their knowledge base, improving their manufacturing process, and embodying the “lightspeed” mentality.
“I’m proud of our team and our ability to face any kind of challenge,” Megan says. “Everyone has different strengths, so we come together and agree on who’s taking what action to resolve any problems that come our way. And we take those lessons for whatever comes next.”