Accelerating the impact our medicines and vaccines can have for patients means not only developing the right products, but also producing and delivering quality products quickly and efficiently.
In recent years, Pfizer has made significant advances in our manufacturing and supply chain. In 2016, we enabled even more efficient product delivery by applying the latest technologies and innovative partnerships to our manufacturing processes and supply chain.
Customizing Manufacturing to Speed Medicine to Patients
Partnerships allow Pfizer to create manufacturing systems that meet the needs of today’s patient
Not long ago, the biopharmaceutical industry relied almost entirely on a complex process that demanded dedicated manufacturing facilities to manufacture large quantities of products. In light of the growing focus on precision medicine, the industry is now shifting toward lower-volume products.
Recognizing this emerging trend, Pfizer joined with partner GEA and G-CON Manufacturing to create a first-of-its-kind manufacturing system known as the Portable, Continuous, Miniature and Modular (PCMM) system, which will give Pfizer increased flexibility and speed of production. The system is designed so Pfizer can quickly deliver customized quantities of drugs, using the same equipment for development, clinical trials and commercial manufacturing.
The miniaturized production facility is efficient– taking up less than 70 percent of the space of a traditional facility – and portable, meaning it can be transported to virtually any location in the world, assembled quickly and mobilized to produce what patients need on site. The system can also transform powders into uncoated tablets in minutes, a process that could take days or weeks with previous technology.
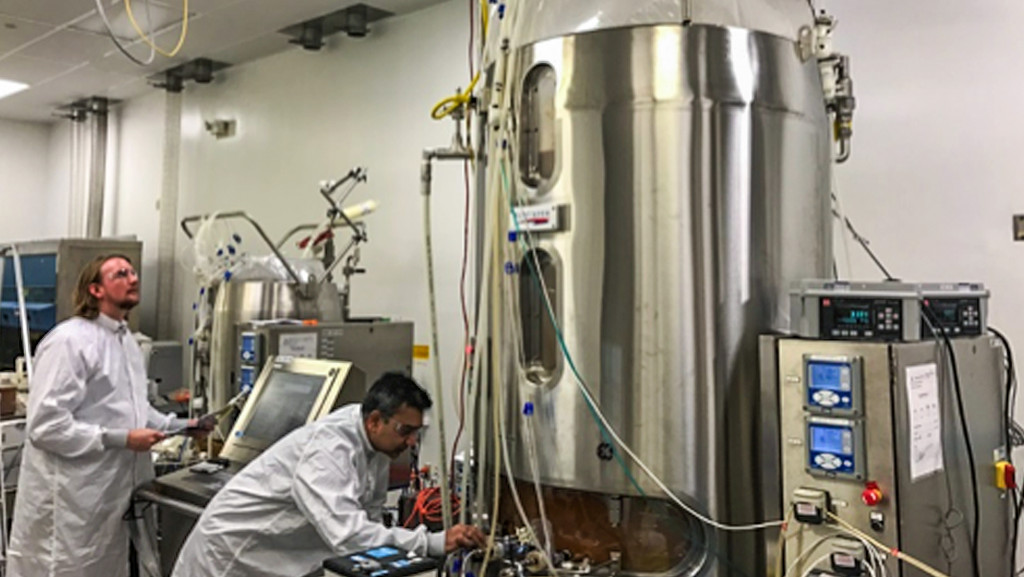
In 2016, Pfizer’s PCMM prototype at our facility in Groton, Conn., became fully operational to manufacture clinical supplies. We also started construction of a commercial PCMM in Freiburg, Germany, which is planned to come online in early 2018. With PCMM, Pfizer and its partners are leading the way toward smaller, more flexible platform technologies, with the potential to transform the future of pharmaceutical development and manufacturing.
Increasing the Efficiency of Pfizer’s Supply Chain
Innovation and intelligence are the backbone of Pfizer
The supply chain is the engine that ensures each step of the pharmaceutical process – from raw material acquisition to the demand signal from the customer to manufacture and patient use – is effective and efficient. Few innovations have had such a dramatic impact on our supply chain as the Highly Orchestrated Supply Network (HOSuN).
Introduced in 2015, HOSuN fuses our global physical supply chain with a global information supply chain, enabling complete visibility into the status of products at all times. This, in turn, makes our management of the supply process more efficient.
Through HOSuN, we can also use predictive analytics to anticipate future demand patterns, as well as supply and delivery needs. This knowledge is crucial for the efficient production and distribution of biologic and vaccine products, for example, which can often take nine to 15 months to manufacture. HOSuN allows us to immediately identify demand – from anywhere in the world – and quickly alert the best production facility to manufacture the product to meet that demand and ensure it is delivered on time.